Lac Design Tool For Building Material Selection
Abstract
Sustainability of current and new developments has become a major issue facing policymakers, developers, city and urban planners, and designers worldwide. Each new construction project entails, among others, the use of natural materials and the consumption of energy, which have a tremendous impact on the built environment over decades, and their environmental consequences only become fully apparent to future generations. The impact of construction projects on environment is especially significant in developing countries. The deterioration of building systems – including building materials – attributes to the economic, cultural and environmental problem, which is related to and affects the sustainable development of any society. In addition, developing countries have suffered for a long time from overlooking or underestimating the basic requirements that must be considered for designing sustainable developments. This article attempts to propose a practical solution for designing sustainable developments by focusing on the building as the primary unit. First, this article presents the requirements for designing a sustainable building, as well as the current process for selecting sustainable building systems and materials. Second, this article describes the Value Engineering program, including the different phases of the job plan. Finally, this article proposes a method for improving building sustainability. The proposed method utilizes the job plan of the Value Engineering program – together with a database that contains up-to-date information on construction systems and materials – as a gear for studying and analyzing the sustainability requirements.
INTRODUCTION
'Sustainable development is the development which meets the needs of the present without compromising the ability of future generation to meet their own needs' (AIA, 2006).
It is the development that fulfills the needs of the present generation without compromising the ability of the future generation to meet their own needs, regardless of setting aims because the continuation of the development is the most important aim.
In this definition, development implies two major concepts, which are not limited to a number of disciplines or areas.
Those two concepts are:
-
The concept of needs: this includes saving and maintaining an acceptable life standard for all people. It is well known that the basic needs for humans are: food, clothing, housing and employment. And, of course, it is the right of every individual to have the opportunity to try hard to raise his or her standard of living higher than this absolute minimum.
-
The concept of limits: this means the capacity of the environment to fulfill the needs present and the future, which are determined by technology and social organizations.
These limits are not only natural limitations such as finite resources, but also the declining productivity caused by overexploitation of resources aside from declining water quality and shrinking biodiversity.
Therefore, it is better for a bright future that needs should be fulfilled and increased to satisfy the requirements of the society. On the other hand, limits should be decreased.
In conclusion, we can safely say that all political, technical and social development can easily be evaluated on the basis of sustainable development. Once more, any development should help fulfill needs and should not increase limitations (see Figure 1).
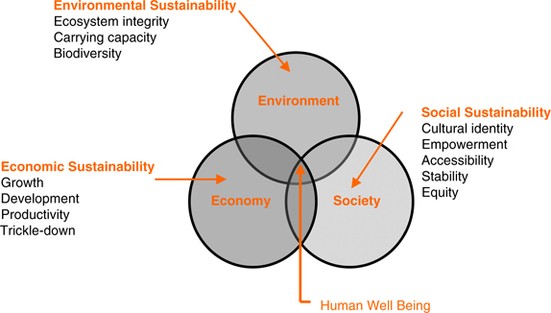
Sustainable development.
Full size image
BUILDING SUSTAINABILITY
A sustainable building is one in which technology and practice meets the multiple requirements of the people and society in an optimal way during the life cycle of the building facility (AIA, 2006). Factors that affect the design of a sustainable building include Economy, Functionality, Durability, Aesthetics, Ecology, Health and Sociocultural aspects (see Figure 2).
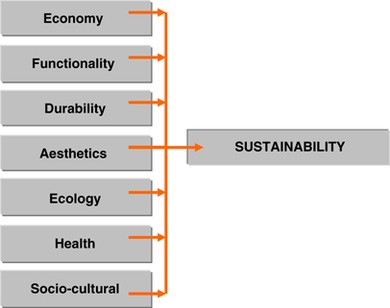
Factors affecting sustainability. Source: By the researcher.
Full size image
The designer needs to consider all these factors in order to design a sustainable building.
The problem of designing sustainable buildings in developing countries has been identified by different researchers and summarized by Makenya and Soronis (1999) as follows: lack of innovation in sustainable and durable materials. Another problem is that local professionals do not encourage the use of those sustainable building systems that are durable and environmentally friendly. In addition, local building regulations, standards and specifications are not sufficient to enable the evaluation of building systems from a sustainability point of view.
Studies such as this one imply that a good part of the building sustainability problem can be attributed to the decisions made during the design phase. In addition, research on building failures in traditional buildings showed that incidence of failure was attributed in 50 per cent of cases to design faults (AIA, 2006).
THE SELECTION OF SUSTAINABLE BUILDING SYSTEMS
During the design process, one of the main decisions that has a great impact on designing a sustainable building is the selection of systems and materials. Every day, the number of potential materials is increasing and new products are introduced in response to competition, new regulations and changes in architectural fashion are produced. In addition, existing products are subjected to constant improvements in order to prolong their life on the market.
Owing to the new and improved products, the architect has too many choices during the selection process. It then becomes impossible for architects to keep track of all new products introduced to the market unless they possess a large database, with continuous updates, to assist them in making the right choices.
The current process for selecting building materials depends on a research study on the kind of building materials which architects select (AIA, 2006).
The research concluded that architects select materials drawn from their personal collection of literature, their own knowledge on what is available in the local and international market, and frequently use short cuts based on their own experience in order to save time. They prefer to stick to familiar products and have a strong preference for certain materials and components that they had used previously. As they do not have the time or energy to research new materials, architects refuse to use new products unless they are unavoidable. Furthermore, architects do not usually consider the different requirements for designing a sustainable building while selecting required systems and materials. The architect mainly focuses on the aesthetic of the alternatives more than any other factor. Therefore, a need exists to adopt more practical and effective approaches to assist architects in selecting sustainable systems and materials.
VALUE ENGINEERING
Value Engineering may be defined as 'the conscious systematic application of a set of techniques that identify needed functions, establish values for these functions and develop alternatives to perform these functions for minimum cost'. Different synonymous terms such as 'Value Management', 'Value Analysis' and 'Value Control' have been used to describe the same approach. Kelly and Male define Value Analysis as 'an organized approach to providing the necessary functions at the lowest cost' or 'an organized approach to the identification and elimination of unnecessary cost'. They also provide different definitions for Value Engineering; the most sound is 'an evaluation of alternative construction materials and systems to save money without major effect on program, maintenance, or appearance, chosen on a priority basis'.
The author interprets Value Engineering as a creative, organized approach that can be applied to the different systems/components of the project, aiming to optimize cost without sacrificing quality. 'Quality' is a term that has many different meanings to different people.
Quality has traditionally been defined either subjectively in terms of 'degree of goodness of excellence'(AIA, 2006), or 'performance to meet the needs of users or customers'(ASCE, 2002); or, objectively, in terms of 'conformance to requirements' (BRE Information et al, 1982).
The essence of the Value Engineering philosophy is to maximize the 'Value' delivered to the owner. In this context, 'Value' expresses three main forms: Cost, Function and Aesthetic.
The Cost of an item is the sum required to produce it or, in other words, is the price paid to get the item. Therefore, if we are comparing two exactly identical items, the one that costs less will have a better value.
The Function is the purpose for which the item exists. For example, the function of glass in a window is protection from the outside environment while enabling light to pass through. Therefore, a functional item is designed primarily in accordance with the requirements of use. Some items may have great costs but little function in the project. These are the items that should be mainly considered during the Value Engineering program because they add little or no value to the project.
The Aesthetic value of an item is reflected in the appearance/attractiveness of the item. Depending on the client's preference, the appearance of a product may be of high priority, and may add enormous value to the project.
In general, when applying a Value Engineering approach, architects have to maintain proper balance between cost, function and appearance in order to obtain the best value. Any unnecessary cost, which provides neither function/use nor appearance, must be eliminated.
HOW DOES VALUE ENGINEERING WORK?
We use the Value Engineering Job Plan, a systematic approach in five phases, which analyzes a project in terms of its functions. The five phases are:
- 1
Information Phase, in which we study documents, learn background, identify functions and identify cost/worth of functions.
- 2
Speculation Phase, in which we identify what else can achieve what must be done. Free use of imagination with no judgment is essential.
- 3
Analysis Phase, in which we rank alternative solutions in terms of quality with realistic judgment.
- 4
Development Phase, in which we develop the details of best alternatives into written proposals.
- 5
Implementation Phase, in which we try to sell proposals to the client and, include accepted proposals in the project.
THE JOB PLAN
In order to study value at any of the project phases and implement the Value Engineering approach, a logical, sequential framework is applied (Figure 3).
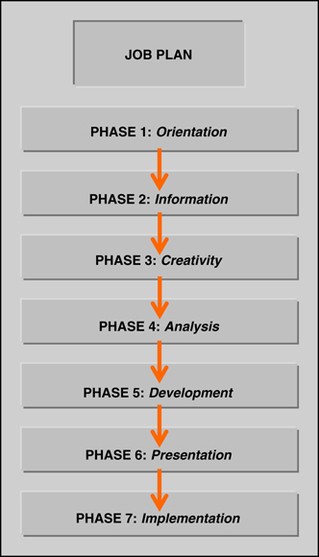
Phases of the job plan. Source: By the researcher.
Full size image
This framework is called the job plan and is derived from Miles' 1961 job plan (AIA, 2006). A summary of the job plan phases is presented below:
The first phase of the job plan is the orientation, or selection phase, in which the client, or decision maker, identifies the main objectives, as well as possible areas of investigation, and the analysis team is appointed, and the strategy plan developed.
The second phase of the job plan is the Information phase and includes gathering the required data. All drawings, specifications, manufacturing methods, samples and prototypes are secured.
Various project systems and their components are identified and arranged in order of priority based on their potential improvement or saving.
The third phase – Speculation or Creativity – deals with identifying different alternatives and possible solutions through brainstorming sessions.
The Analysis phase is the fourth phase, which follows and consists of determining the technical and economical aspects of each alternative. The cost of each element is identified, as well as whether it will perform the basic function require of it or not.
The fifth phase – Development – includes the detailed investigation of the requirement ideas selected during the previous phase in order to determine their technical and economic feasibility. The selected ideas should then be translated into meaningful design solutions.
The sixth phase of the job plan carries a formal Presentation of the refined ideas supported by drawings, specifications and cost to the decision makers, with a highlight on advantages and disadvantages of the proposed solution. This phase is vital to the success of the Value Engineering program, as one of the main obstacles to implementing a Value Engineering system is the designers' resistance. Usually, designers do not accept any alterations or modifications to be made to their designs, and thus do not appreciate the proposed ideas. It is the job of the Value Engineering team to use diplomacy and argument to convince designers of the merit of using the alternate solution.
Finally, the last phase includes the implementation of the proposed solution and a follow-up procedure to ensure effectiveness of the solution. Feedback from all project participants should be encouraged.
VALUE ENGINEERING DURING THE DESIGN PHASE
Value Engineering may be implemented throughout the different project phases, starting from the conceptual planning phase until to the construction phase. However, Value Engineering applied at the early phases of a project, especially during the design phase, will realize the greatest benefit. Several researches, summarized by Kelly and Male (2004), concluded that the optimum locus to conduct a Value Engineering analysis is when the design is 35 per cent completed – or after the development of the schematic design – as all costing data will be more readily available in the form of the cost estimate, and therefore savings can easily be identified.
Furthermore, any changes to design are easily introduced at this point. During this phase, the design team investigates alternate design solutions and alternate materials and systems. Value Engineering analysis made during this phase will focus on studying the major systems of the project. For example, the Value Engineering team may study the appropriate conveying system for the project (the use of elevators or escalators) or the proper façade covering material and so on.
During the detailed design phase, the design team evaluates, selects and finalizes the detailed systems and components of the project, and prepares the technical documents, specifications and general conditions. Implementing the Value Engineering program is also very significant at this phase as it may be applied to specific systems within the project, and even at different levels within the system until reaching the subsystem and the component levels of the project. The Value Engineering team will look more into the details of the selected systems and materials. For example, it is not unusual to study the 'door' knob' component as part of a Value Engineering program for a hotel project.
IMPROVING BUILDING SUSTAINABILITY
The application of the Value Engineering approach during the design phase may be adapted and utilized to improve building sustainability. As noted earlier, Value Engineering mainly focuses on the 'Value' delivered to the owner, which is expressed in Cost, Function and Aesthetic forms. Meanwhile, factors affecting the design of a sustainable building include Durability, Ecology, Health and Sociocultural factors, in addition to Economy, Functionality and Aesthetics. If the Value Engineering team is able to consider the remaining sustainability factors during the application of the Value Engineering 'Job Plan', the result should not only be the increase in the 'Value' delivered to the owner, but also a sustainable building that fulfills the different sustainability requirements.
The following method is proposed to enable the Value Engineering team to consider all sustainability factors. The method consists of two main modules: a 'Systems database' module and the 'Job Plan' module (Figure 4).
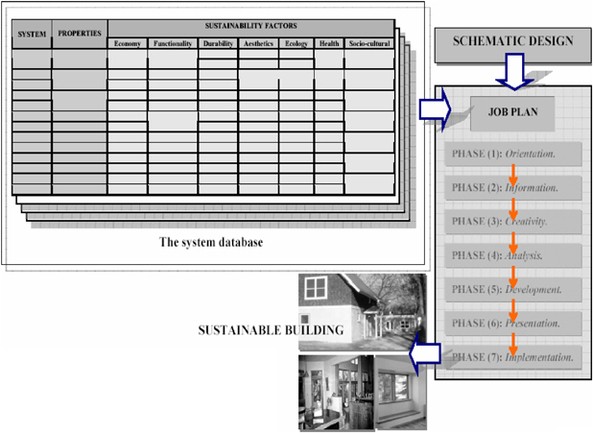
Proposed method for sustainability improvement. Source: By the researcher.
Full size image
The first module consists of a database that contains various systems and materials. The database will assist in presenting the information required during the Value Engineering analysis in an easy-to-comprehend way. The database contains numerous records, with each record detailing system properties such as its length, width, height, available colors and so on.
The record also includes the system's compliance with the different sustainability requirements. For example, for a specific flooring system, the record's fields will demonstrate how much it will cost, how durable it is, its expected life before requiring maintenance, its impact on health and so on. A rating system should be developed to evaluate each factor, and hence to enable the decision makers to make the right choice.
The 'Job Plan' module was discussed earlier for the Value Engineering approach. The same seven phases will be used to analyze the design, and to present and propose a refined design for a sustainable building. The adaptation will occur mainly in the factors they consider and the means in which the information is presented. The Value Engineering team will have to consider more factors (Durability, Ecology, Health and Sociocultural) during the job plan phases. The systems' database will assist in presenting the required information in an enhanced way instead of relying only on the Value Engineering team's knowledge.
The following examples (Figure 5) illustrate how Value Engineering has increased the sustainability of buildings:
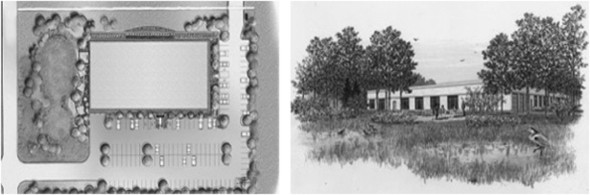
Mannik and Smith Professional Office Building (http://www.walbridge.com/index.cfm/Projects). Owner: 1800 Haggerty Road LLC; Location: Canton, MI; Market: Office; Service: Design-Build; Size: 29 101 square feet; Region: Midwest; Design Partner: David Gebhardt Architects.
Full size image
Overview
Walbridge was selected to perform design-build services on the Mannik and Smith Professional Office Building. The 29 000 square-foot sustainable building provides office and lab testing space with additional shell space for future tenant build out. The Walbridge team helped reduce site disturbances, utilized local materials to minimize effects of transportation on the environment, and recycled construction waste. Systems were created to manage storm water, reduce light pollution, reduce water use throughout the facility and optimize energy. An indoor air-quality management plan was utilized, preventing residual indoor air quality issues and protecting on-site workers. In addition, low emitting materials were used. The project is registered with the USGBC, and intends to pursue LEED® certification.
Overview
Walbridge was construction manager of a new utility infrastructure for historic Greenfield Village (Figure 6). The project included electricity, natural gas, water and storm sewer, security wiring and communications. In addition to installing 300 new streetlights, Walbridge relocated 12 of the historic buildings, renovated the village store and gatehouse, and built the crafts and trades buildings and catering pavilion. Walbridge provided $1.85 million in Value Engineering ideas, and accommodated 34 design revisions throughout construction. Greenfield Village, part of The Henry Ford campus, is a National Historic Landmark. Built in 1929, it is the nation's largest outdoor museum and welcomes 1.5 million visitors annually.
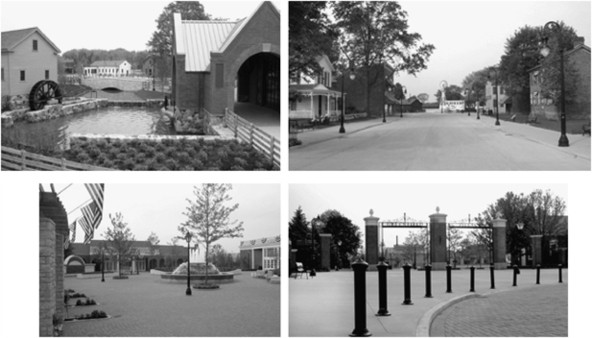
Greenfield Village restoration (http://www.walbridge.com/index.cfm/Projects). Owner: The Henry Ford; Location: Dearborn, MI; Market: Cultural; Service: Construction Management, Walbridge Equipment Installation; Size: 80 acres; Region: Midwest; Design Partner: JGA, Inc. ARCADIS Grissim Metz Andriese Associates; Awards: Outstanding Achievement – Themed Entertainment Association.
Full size image
Overview
Walbridge was the construction manager for Visteon's new 870 000 square-foot, LEED®-certified corporate headquarters and innovation center in Van Buren Township, Michigan. Visteon Village (Figure 7) was a complex project that required Walbridge's expertise to control cost and timely delivery of large-scale, multi-phased projects. The move consolidated 3200 employees from 13 facilities to make operations more efficient and cost-effective, while enhancing product innovation.
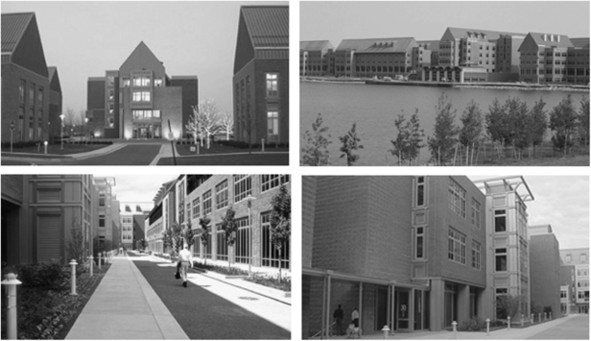
Visteon village (http://www.walbridge.com/index.cfm/Projects). Owner: Visteon Corporation; Location: Van Buren Township, MI; Market: Office; Service: Construction Management; Size: 870 000 square feet; Region: Midwest; Design Partner: Smith Group; Awards: Sustainability Design Award – American Institute of Architects 2006 Honor Award – American Institute of Architects Construction and Design Award – ASHRAE Detroit Chapter 2006 Construction and Design Excellence Award – ESD.
Full size image
The 265-acre site is surrounded by heavily wooded and wetland areas. Visteon Village has nine separate facilities for office, manufacturing and technical spaces. A Village Center overlooks a 37-acre, man-made lake. The center houses presentation and training areas, product displays, IT functions, and a cafeteria. The center of the complex is lined with shops, sidewalks, trees and benches, creating a main street feel.
To promote a close-knit working environment among the village's employees, the buildings are close together, no higher than four stories and no wider than 60 feet. The workspaces are less enclosed than typical cubicles, with shorter walls and wide, open entrances. Many are situated in front of windows to take advantage of natural light and foster creative thinking. Product development workflow was a design focus, creating adjacencies among product development and cross-functional teams. Advance product engineers are located together, fostering an information flow throughout the product lines.
The project's most notable challenge was managing the daily workforce increase. The multiple-building, fast-track project required trades to work simultaneously in the same areas. The project man-hour volume set record levels, with 12 straight months totaling over 1 503 294 man hours worked. Visteon established a staged/phased personnel move-in while workers were still on site. Visteon Village was delivered on time and was completed under budget. Visteon constructed a medical/fitness center and IT infrastructure improvements with budget savings.
Throughout the project, the team used unique engineering and construction techniques. In areas of concentrated rubble, soil was removed and deep dynamic compaction took place. The construction team also undercut significant portions of the site to remove and relocate earth and existing rubble material to backfill 'borrow' and 'pond' areas. Creating the lake water intake system involved special piling, deep pit and trench excavation, barge-mounted crane activities and dewatering. Lake-edge slopes comprised highly unstable fill soils and limited development and required stabilization. Lake edges were stabilized using a combination of stone riprap, sheet piling and graded and planted slopes.
The Visteon Village project achieved LEED certification by the US Green Building Council. Over 35 acres of woodland and wetland area were preserved during construction. Boardwalks and a nature trail were constructed for employee use. Recycled material, including 75 000 tons of recycled concrete, composed 75 per cent of the material used to build the campus. Five thousand trees were planted to enhance the environment. A perimeter wetland zone around the lake was established to attract waterfowl. In summer months, a chilled-water intake loop in the 65-foot-deep lake cools the buildings. The open office plan, with only 20 closed-wall offices, features extensive daylighting. To conserve energy consumption, advanced, efficient technology was incorporated into all major building systems.
GENERAL RECOMMENDATION
-
Take a holistic, life-cycle approach to planning, design, costing, construction, and maintenance and building management.
-
Maximize the reuse and redevelopment of existing built infrastructure and consider non-building service delivery options.
-
Maximize the use of passive design principles, for example natural daylight, natural ventilation, solar and thermal mass.
-
Design any modification work for ease of future adaptability.
-
Maximize the use of existing, renewable, recyclable resources and locally sourced resources.
-
Minimize waste to landfill from construction, modification/refurbishment and maintenance activities.
-
Minimize air pollution/emissions from buildings, for example ozone depleting substances (Chlorofluorocarbons (CFC) and Hydro chlorofluorocarbons (HCFC)), greenhouse warming gases (Carbon Dioxide (CO2) and oxides of Nitrogen (NOx)) and Volatile Organic Compounds (VOCs).
-
Minimize resource consumption, for example materials, water and energy in the operation of the building.
-
Minimize impact on the environment and preserve/support/re-establish physical viability, biodiversity and natural ecosystems.
-
Monitor and review strategies established to minimize the environmental impact during design, construction, maintenance, demolition and deconstruction activities.
CONCLUSION
Improving building sustainability requires unifying efforts of all involved parties.
Practical approaches need to be developed. Policymakers should draft laws that imply the use of sustainable systems and materials. Owners should also demand their designers to use more sustainable systems. Architects are required to consider the various factors for designing sustainable buildings, and to encourage the implementation of effective approaches for the enhancement of their designs.
This article has presented a method to assist in designing sustainable buildings. The Value Engineering approach and a database of available systems with classification of how each system complies with the different sustainability factors are proposed to be used during the system's selection process. The key issue is to update the database on a regular basis with new and improved systems and materials.
This will enable designers to have up-to-date knowledge on what is available in the market, how much it costs, how durable the product is, as well as its impact on the environment, thereby enabling them to design sustainable buildings.
References
-
American Institute of Architects (AIA). (2006) Value engineering's history in construction.
-
ASCE – American Society of Civil Engineers. (2002) Quality in the Constructed Project, A guideline for Owners, Designers, and Constructors, Vol. 1, New York: ASCE.
-
BRE Information. 18/82, Bonshor, R.B. and Harrison, H.W. (1982) Traditional housing: A BRE study of quality – UK.
-
Kelly, J. and Male, S. (2004) Value Management in Design and Construction – The Economic Management of Projects. London: E & FN Spon.
Google Scholar
-
Makenya, A.R. and Soronis, G. (1999) Designing for sustainable buildings in developing countries – Problems and priorities. 8DBMC – Proceedings of the Eighth International Conference on Durability of Building Materials and Components; 30 May – 3 June, Vancouver, Canada.
Download references
Rights and permissions
About this article
Cite this article
El-Alfy, A. Design of sustainable buildings through Value Engineering. J Build Apprais 6, 69–79 (2010). https://doi.org/10.1057/jba.2010.14
Download citation
-
Received:
-
Revised:
-
Published:
-
Issue Date:
-
DOI : https://doi.org/10.1057/jba.2010.14
Keywords
- sustainability
- Value Engineering
- built environmental
- job plan
- building system
- building materials
Lac Design Tool For Building Material Selection
Source: https://link.springer.com/article/10.1057/jba.2010.14
Posted by: lockefrouleem.blogspot.com
0 Response to "Lac Design Tool For Building Material Selection"
Post a Comment